Each Producer will submit copies to NCDOT of all final QC and QA verification test report forms, COA’s, and COC’s used with the Producer’s QC plan or with this QC/QA plan. Test reports, including IA, shall contain at a minimum the following information:
A. Certifying statement with signature on the test report or COC/COA. This statement must read as follows:
“By providing this data under my signature, I attest to the accuracy and validity of the data contained on this form and certify that no deliberate misrepresentation of test results, in any manner, has occurred.”
B. Name and address of the testing laboratory.
C. The facility or terminal who owns the sample.
D. Unique report identification number and/or title and the date issued.
E. Identification of the NCDOT QC or QA verification North Carolina batch number.
F. Description, identification, and condition of the test sample.
G. Date and time the sample was taken.
H. Sampled By.
I. Tank or car number.
J. Grade of asphalt that is being tested.
K. Date of receipt of the test sample.
L. Date(s) of test completion.
M. Identification of the standard test method used and a notation of all known deviations from the test method.
N. Test results and other pertinent data required by the standard test method.
O. Identification of any test results obtained by a subcontractor and the name of the subcontractor.
P. Name of the person(s) accepting technical responsibility for the test report.
Q. Technician’s name
R. Signature.
S. Certifying statement that the material meets AASHTO specifications.
T. Certifying statement that the material DOES NOT MEET SPECIFICATIONS OR TRUE GRADING when a high temperature true grade is performed and is out of range or other deviation from specifications. See
Section III (C)(3).
I. NCDOT HiCAMS Sample Card
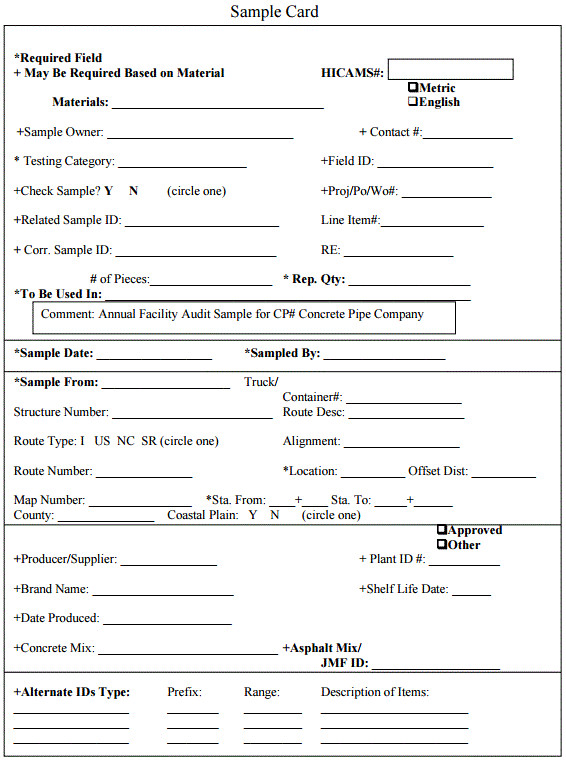
II. Requirements for Producer Sampling Log and Lab Report
The minimum information required is as follows:
1. Terminal name and location
2. Tank Number
3. Performance Grade
4. Date
5. Time
6. NCDOT QC- or NCDOT IA-
7. Flashpoint
8. Rotational Viscosity @135° C
9. DSR on Original @ required Temperature(s).
10. DSR Temperature
11. Mass Loss Percent
12. DSR on RTFO @ required temperature(s)
13. DSR on PAV @ required temperature(s)
14. Pass/Fail Temperature (High End Grade)
15. BBR on PAV @ required temperature(s)
Optional Fields Below:
16. Specific Gravity @ 60°F
17. Elastic Recovery
18. Direct Tension @ required temperature(s)
19. Absolute Viscosity @ 140°F
20. Penetration 2 hrs or 4 hrs
21. Terminal / Refinery Lot No.
APPENDIX VIII: TECHNICIAN TRAINING AND EVALUATION RECORD
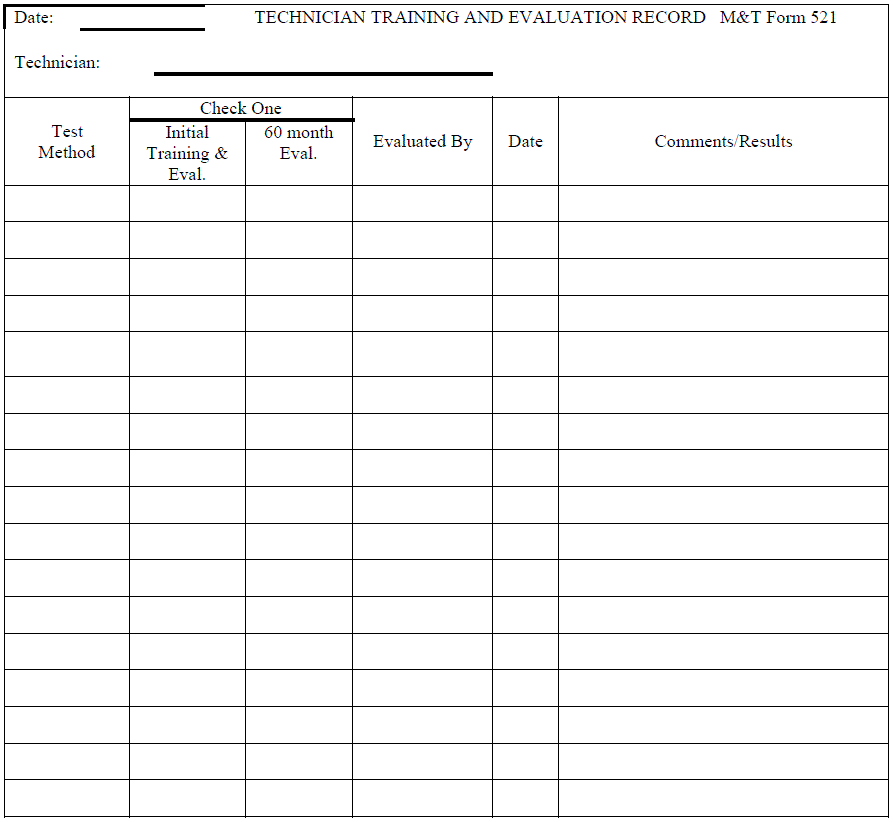
APPENDIX IX: PRODUCER HISTORICAL ACCEPTANCE LIMITS FOR PGAB TEST METHODS
This is an EXAMPLE ONLY of typical producer specific acceptable limits.
APPENDIX X: FEDERAL HIGHWAY ADMINISTRATION POSTER
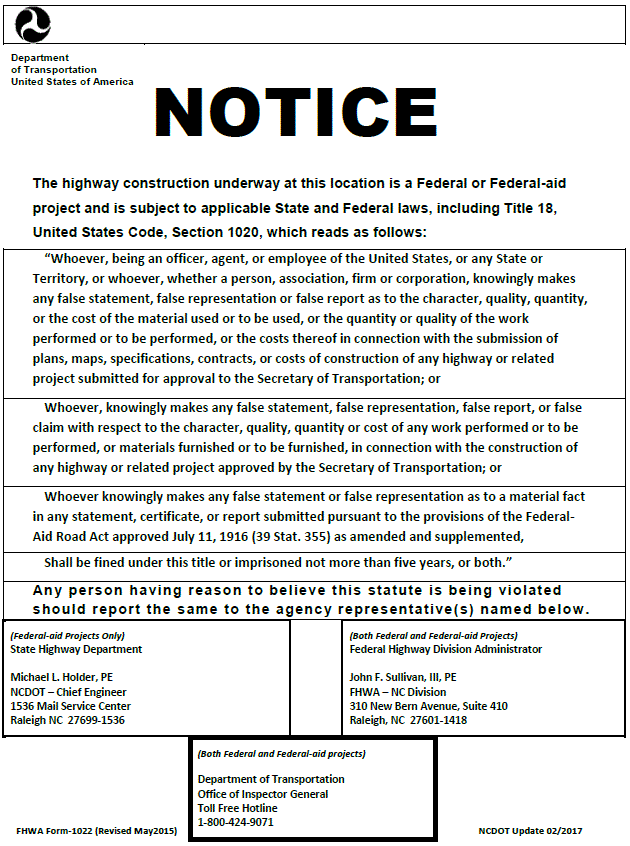
APPENDIX XI: SPREADSHEET FOR PGAB TEST DATA FOR SUBMITTING TO NCDOT
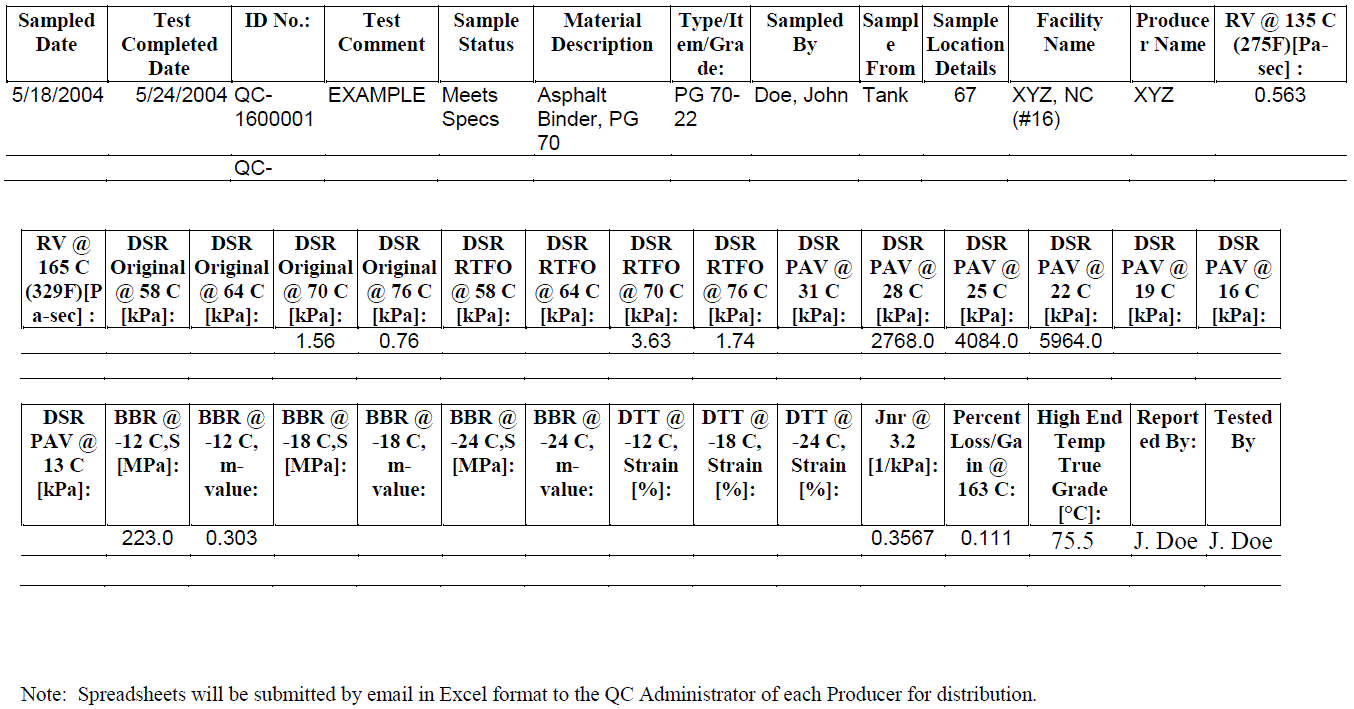