Before installation begins, furnish the following pavement marking material certifications in accordance with
Article 106-3:
Any questions concerning the historical performance and approval status of a pavement marking material should be directed to the
Signing and Delineation Unit.
1205-3 CONSTRUCTION METHODS
Definitions:
Premarking (could also be referred to as layout by some Contractors):
Small paint spots used by striping Contractors to establish locations of pavement markings (i.e., lane widths, stop bar locations, arrow locations, etc.) are also used to guide the striping equipment for alignment. This is not a pay item, but is a requirement for proper installation of all pavement markings. Premarking must be inspected and approved prior to the installation of pavement markings.
Interim paint:
A thin layer of pavement marking paint applied at the striping Contractor's option, in lieu of durable pavement markings to comply with time limitations for placement of pavement markings or to prevent exposure of durable markings to ongoing construction traffic (i.e., tack trucks and tack from dump trucks). The width of the interim marking shall be no more than
1/4" less than the specified line width. Interim marking should be overlaid with the durable marking within
30 days. If interim marking is placed on concrete, remove
100% of the paint prior to placing polyurea. When interim paint marking is placed on concrete, such as diamond grinding projects, a pay item should be included for the paint marking.
Pavement marking lines, paint:
-
Temporary paint markings - Used on construction projects for detours, lane shifts, and lifts of asphalt other than the final pavement surface. Used on resurfacing projects on milled surfaces and lifts of asphalt other than the final pavement surface. When placing
two applications, pay for each acceptable application.
-
Permanent paint markings - Used on construction projects and resurfacing projects when durable markings are not used. (Generally on -Y-lines and secondary roads.) When placing
two applications, pay for each acceptable application.
See inspection procedure “INSPECTION OF IN-PLACE PAVEMENT MARKING MATERIALS" at the end of this section. Any questions regarding the procedure shall be directed to the
Signing and Delineation Unit.
(B) APPLICATION EQUIPMENT
Glass Bead Dispensing Equipment:
Placing Drop-On beads on long-line pavement marking shall not be done by gravitational methods or dropping by hand. Bead dispensing by gravitational methods is acceptable on characters, symbols, or short-line markings when using handliners with a functioning bead dispenser.
Bead dispensing by a straight mechanical feed may result in lower retroreflectivity readings than if a pressurized mechanical feed system is used. Bead installation inspection should be performed as the beads are being placed.
(C) WEATHER LIMITATIONS AND SEASONAL LIMITATIONS FOR ALL MARKINGS
All pavement marking materials can be affected by adverse climatic conditions. As favorable weather conditions deteriorate be prepared to stop pavement marking operations. Refer to Section 1205 for seasonal limitations guidance for each material to be used. Contact the
Signing and Delineation Unit for guidance with acceptable alternatives.
(D) TIME LIMITATIONS FOR PLACEMENT AND REPLACEMENT
For any critical paving operation, such as a tie-in, adequate time should
be provided during each work period for the placement of pavement markings. Place temporary paint
to achieve time limitations in Table 1205-1 when the final pavement markings cannot
be placed.
(E) PREMARKING / INTERIM / TEMPORARY MARKINGS
A good resource for assistance with pavement marking or premarking is the Traffic Services Supervisor or the Paint Crew Leader, especially for passing and no passing zones on two-lane roadways.
If the pavement marking design does not match the field conditions, contact the Division Traffic Engineer and the
Signing and Delineation Unit.
The Contractor shall reference the existing markings prior to the markings being obliterated and make that information available to the Engineer. Special attention should be placed on retracing operations when dealing with multi-lane roads or roads with widening on one or both sides. A videotape of the area is a good way to record the existing pavement markings.
Every line should be premarked to establish proper lane widths and locations.
(F) SURFACE PREPARATION AND CURING COMPOUND AND SILANE REMOVAL
Clean all surfaces in accordance with the Specifications. Any type of curing compound and/or Silane treatment needs to be removed
two inches wider than the line that is to be placed. Acceptable methods of curing compound or Silane treatment removal include grinding and high-pressure water blasting.
Curing compound should be removed when installing temporary paint for patterns that will be in place more than
90 days.
Curing compound is not typically used on bridge decks. However, the bridge deck could have a Silane treatment and will have surface laitance and residue that will need to be removed prior to placing the final markings. This is especially important for polyurea. If the surface residue or laitance is not removed, the pavement marking, especially polyurea, will pull the surface laitance from the bridge deck and the marking will debond. Many bridge decks are mechanically grooved, which may require water blasting to ensure all essential surface laitance is removed for the markings to properly bond. This is incidental to the cost of the markings and should not be paid for with the curing compound removal pay item.
The Department does not typically use thermoplastic on concrete. However, there are occasions on short bridge projects thermoplastic is striped across the concrete bridge deck. If this situation occurs, ensure primer sealer is placed prior to installing the thermoplastic markings.
It is extremely important the Contractor and Inspector perform in-place inspection as the marking is being applied instead of waiting until all of the marking has been placed. Ideally, the inspection should be done in the first
few hundred feet and routinely throughout the operation of each day’s placement to detect any problems early. This inspection will greatly reduce problems that arise after improper placement of pavement markings. The mil thickness of liquid materials such as polyurea, epoxy and paint can affect the retro-reflectivity and can be challenging to inspect. This must be inspected while the material is wet and as the material is sprayed, but prior to the installation of beads. A flat piece of metal should be placed between the material and bead guns and quickly removed after the material gun passes over it. Then, using a wet film thickness gauge, check the mil thickness. If the material is too thin, it could still meet the
30-day retro-reflectivity, but will fall fast and not provide the expected life-cycle since there is not enough binder material to hold the beads. On the other hand, if the liquid material is too thick, it could have below minimum retro-reflectivity but will increase over time and be the better line. It is always better to have the material too thick than too thin.
If you are having problems with compliance of the initial readings, thickness and/or retro-reflectivity, contact the
Signing and Delineation Unit.
Night inspections should be made during the 30 day application review to note any problems.
Most markings reflectivity readings will increase within a
few weeks. On the day of application, take reflectivity measurements after the marking has completely cured and the thermoplastic has completely cooled. As the thermoplastic cools the color will change and the readings will increase.
Historical data tells us if there is going to be a problem with retro-reflectivity, it will typically occur within
30 days of placement. Checking the retro-reflectivity and bond during this time allows us to make sure the product will provide good service life. The retro-reflectivity may be checked for trouble shooting the same day the line is installed. However, the optimum time to check this requirement is between
15 and 30 days of final marking placement. If it is not possible to check the retro-reflectivity using an approved hand held device, contact the Signing and Delineation Unit for the mobile retro-reflectivity device. The Signing and Delineation Unit should be contacted at least
thirty days prior to the marking being placed.
When checking the retro-reflectivity, there may be a section(s) of a line that does not meet the minimum retro-reflectivity requirements. A section of line is defined as
1000’ of marking. If using a hand held device, take six readings within a
10’ area every
500’ and average the numbers to get the
500’ retro-reflectivity average. Go another
500’ and repeat the process. Once you have taken readings in the
1000’ section, average those readings together and that is your average for the
1000’ section.
If a mobile retro-reflectivity device is used, the readings will come from the Signing and Delineation Unit. These readings are automatically averaged every tenth of a mile. However, the same inspection applies to the mobile readings as described above.
If it is determined the marking has attained the minimum
30-day retro-reflectometer readings, the material has bonded correctly and workmanship is satisfactory, go ahead and pay full payment. However, continue to watch for debonding and discoloration within the
12 month observation period per
Subarticle 1205-3(H).
Article 105-3 applies to all pavement marking, but use the guide below to make the determination of acceptable damages and for statewide consistency. If any section of a line has not attained the minimum 30-day retroreflectometer readings (mcd/lux/m2) within 30 days of acceptance see the following:
NOTE: The pavement marking contractors are not responsible for situations such as snowplows and tracking of asphalt on the markings that could result in debonding or lowering the retro-reflectivity.
THERMOPLASTIC WITH STANDARD BEADS
-
Level 1: Retroreflectivity is between 375 and 350 for white and 250 and 225 for yellow, you may contact the Area Construction Engineer for assistance in determining if the marking may have future retroreflectivity and debonding issues. If no problem is identified, you may go ahead and pay full payment. Evaluate the marking again prior to the end of the 12 month observation period for debonding and discoloration.
-
Level 2: Retroreflectivity is between 349 and 325 for white and 224 and 200 for yellow, contact the Signing and Delineation Unit and Area Construction Engineer for assistance in determining if the marking may have future retro-reflectivity and debonding issues. If it is determined the marking can provide an adequate service life, take a 10% pay reduction for the failing section(s). Evaluate the marking prior to the end of the 12 month observation period for debonding and discoloration.
-
Level 3: Retroreflectivity is between 324 and 305 for white and 199 and 180 for yellow, contact the Signing and Delineation Unit and Area Construction Engineer for assistance in determining the cause of the low retro-reflectivity and determining if the marking may have future retro-reflectivity and debonding issues. If it is determined the marking can provide an adequate service life, take a 25% reduction for the failing section(s). However, if it is determined the line cannot provide any acceptable service life, it may be required to remove and replace the section(s) of marking. This will be a collective decision between the Division, Signing and Delineation Unit and the Construction Unit (Area Construction Engineer.)
Workmanship or visual quality of a line may also justify a price reduction in addition to poor retroreflectivity. This could be due to lateral deviation of the long-line, messy work, removing markings that are not in the correct location and damaging the roadway, etc. Determining the quality of the workmanship is more subjective than retro-reflectivity or bonding issues. Typically, a price reduction of
5% to 10% is taken due to poor workmanship for a segment(s) of line or characters/symbols. All workmanship reductions/removals should be discussed collectively by the Division, Signing and Delineation Unit and Construction Unit (Area Construction Engineer.) The Area Construction Engineer will communicate the Department’s final decision to the Resident Engineer by letter.
The same process, evaluation and price reductions apply to markings with
Highly Reflective Media as to marking that is applied with standard beads as described above. The following retro-reflectivity ranges will be used in determining price reductions as in the
three levels described above.
THERMOPLASTIC OR POLYUREA WITH HIGHLY REFLECTIVE MEDIA
Level 1: White 800 to 750 Yellow 600 to 550
Level 2: White 749 to 700 Yellow 549 to 500
Level 3: White 699 to 650 Yellow 499 to 450
(I) REMOVAL OF PAVEMENT MARKINGS
When removing temporary or existing lines, reference 1205-3 (I) of the Standard Specifications for guidance. Pavement markings must be removed by acceptable methods that will not materially or structurally damage the surface of the pavement. General industry practices for removal of marking includes mechanical grinding, high pressure water blasting, and recoverable shot blasting. All these methods will practically have some effect on the pavement. The goal of line removal is an adequate removal with minimal surface affect. For asphalt pavements, do not use high pressure water blasting. When removing markings where the new markings will be placed in the same location, shot blasting or grinding may be the better option. Recoverable shot blasting creates the least amount of debris and possibly the least amount of damage to the pavement, but is more difficult to remove durable markings.
When temporary pavement marking lines are to be removed from concrete pavement, water blasting or grinding is the preferred method. Mechanical grinding is not an acceptable method of pavement marking removal on concrete pavements when the marking to be removed is not in the final location. This usually happens during construction containing temporary traffic shifts. When this occurs, high pressure water blasting is the only acceptable method.
ALL DEBRIS CREATED BY LINE REMOVAL MUST BE VACUUMED AND REMOVED FOR PROPER DISPOSAL. If not completely removed, may cause issues when placing the new markings. When determining the method of line removal, consider the time required for cleanup (drying, sweeping, and vacuuming).
Remove 100% of existing marking prior to placing polyurea for restriping projects. Many times, temporary paint or premarking must be installed before the polyurea on new projects. When temporary marking is installed on concrete, 100% of the temporary marking must be removed before placing polyurea. When temporary paint is installed on asphalt, polyurea can be placed without removing the temporary paint line as long as no more than 5 to 8 mils of paint with 1 to 3 pounds of beads per gallon of paint are installed.
Cold Applied Tapes have the same marking removal and surface preparation requirements as polyurea described above.
Grinding on any pavement scars the pavement surface such that another line is created which may be visible at night and can be confusing to traffic. Take special care not to excessively scar the pavement when removing pavement markings. If a portion of the marking remains after removal on asphalt pavement surfaces and it is enough to mislead traffic, you can use flat black paint to cover it. Refer to
Subarticle 1205-3(I) of the Specifications for more details. Contact the
Signing and Delineation Unit if you have any questions concerning removal of pavement markings.
Removal of temporary tape is incidental to the pay item.
Methods for removal of pavement marking lines should be addressed in the contract and discussed at the preconstruction conference.
In many purchase order pavement marking contracts, removal of lines is incidental to various pavement marking pay items in the contract. However, it is still important the means of removal is identified in the contract.
(J) PAVEMENT MARKING INSTALLER QUALIFICATIONS
Ask for a NC Pavement Marking Certification from at least one person working on each crew. If you have questions about contractors and/or the certified personnel in their company, contact the Signing and Delineation Unit or go to our website at:
1205-4 THERMOPLASTIC (Alkyd/Maleic)
(A) APPLICATION EQUIPMENT
In cool weather, the temperature of the material when it hits the pavement is critical. The temperature measurement for thermoplastic should be taken at the “shoe” or right after it has hit the ground and not in the melting kettle. It is hard to maintain the temperature in secondary kettles, such as pushcarts, particularly in colder weather.
When extrusion equipment is used, the extrusion “shoe” should be checked regularly for wear. The more worn the shoe, the thinner the casters which results in a thinner line extruded.
(B) WEATHER LIMITATIONS AND SEASONAL LIMITATIONS
Only apply thermoplastic pavement markings when the ambient air temperature and the temperature of the pavement is 50°F and rising.
Do not apply thermoplastic pavement markings between the dates specified below:
East of I-95 December 15 and the following March 16
East of I-77 to and including I-95 November 30 and the following April 1
West of and including I-77 November 15 and the following April 16
(C) APPLICATION
Prior to applying the thermoplastic markings, the Contractor has the option to place a dry film thickness of 5 to 8 mils of interim pavement marking paint and includes the application of drop-on glass beads at a rate of 1 to 3 lbs per gallon of paint. If the Contractor elects to do this, they will
not
be compensated. The Contractor must cover the thin layer of pavement marking with thermoplastic pavement marking within 30 days.
Within 30 days of installation, markings should meet the minimum retroflective values shown in
Section 1205-3
(H)(2) Assessing Damages above.
Apply polyurea pavement marking only when the ambient air and pavement surface temperatures are 40°F and rising.
Do not apply polyurea pavement marking between November 15 and the following February 28 unless the surface is free from winter surface treatment applications.
The equipment shall be certified by the manufacturer as suitable for the application of polyurea and reflective media. The striping equipment shall bear a decal identifying it as manufacturer certified. Application equipment is a mobile, truck mounted and self-contained pavement marking machine specifically designed to apply multi-component liquid material, glass beads and reflective media.
Wait
a minimum of 15 days before applying polyurea on new asphalt. The reason for the waiting period is the new asphalt's oils may seep through the polyurea causing it to become darker and discolored. If traffic must be maintained on the roadway during the 15 day waiting period, place a thin layer of paint. There is no compensation for this paint. The dried film thickness of the paint should not exceed 5 to 8 mils and includes the application of drop-on glass beads at a rate of 1 to 3 lbs per gallon of paint. Place polyurea pavement markings within 30 days.
When placing polyurea on new concrete pavement, all curing compound and surface laitance MUST be removed. Polyurea pavement marking lines shall have a minimum dry film thickness of 20 mils (25 mils wet) when placed on concrete or asphalt pavements. The minimum dry film thickness should be increased to 30 mils when applied on textured surfaces such as OGFC.
Within 30 days of installation, markings should meet the minimum retroflective values shown in
Section 1205-3(H)(2) Assessing Damages above.
1205-6 COLD APPLIED PLASTIC
(A) APPLICATION EQUIPMENT
There are three basic types of equipment required to install cold applied plastic: the primer cart, the applicator cart, and the tamper cart.
Proper weight on the tamping machine is an important part of the adhesion process. The tamper cart should be used as the primary method of adhering tape to the roadway. The use of a truck tire for tamping is acceptable but only after the cold applied plastic has been properly tamped with the tamper cart. When vehicle tamping is used, do not turn the wheel of the vehicle when the tire is on the cold applied plastic.
Check that the cold applied plastic was installed per manufacturers' specifications for ambient air temperature and surface temperature.
(B) TYPES OF COLD APPLIED PLASTIC
At the time of installation, cold applied plastic pavement markings shall meet retroreflective values in Table 1205-5.
Type 1 is typically a 2-year life cycle permanent tape used on roadways with an ADT of 5,000 or less.
Type 2 material may come as one piece with a black border with yellow or white in the center. Type 2 is typically a 5-year permanent tape used on roadways with an ADT greater than 5,000.
Type 3 wet reflective tape shall meet Table 1205-5 retroreflective values, both wet and dry.
Type 4 (Removable Tape) should last a minimum of 6 months. If temporary tape is used and comes up within 6 months, the Contractor shall replace the tape at their expense.
1205-7 HEATED-IN-PLACE THERMOPLASTIC
(A) APPLICATION
EQUIPMENT
Applied by using a propane blow-torch per manufacturer's recommendations.
(B) WEATHER LIMITATIONS
Apply heated-in-place thermoplastic only when ambient air temperature and pavement surface temperature is 40°F and rising.
(C) APPLICATIONS
Apply heated-in-place thermoplastic per manufacturer's instructions. Proper heating temperatures, duration of heat application, and clean/dry surfaces are critical to obtaining proper bond of heated-in-place thermoplastic to the roadway. Use a primer sealer per manufacturer's instructions when installing heated-in-place thermoplastic on concrete.
Within the 30 days of installation, markings should meet the minimum retroflective values shown in Section 1205-3(H)(2) Assessing Damages above.
(A) APPLICATION EQUIPMENT
The main determining factor of paint thickness is the speed of the paint truck. Generally, a speed of 10-12 miles
per hour will result in a paint thickness of
15 to 18 mils wet film thickness (without beads). Speeds in excess of
12 miles per hour may not produce
15 mils wet film thickness.
Paint in only recommended for interim and temporary applications. Thermoplastic, polyurea, cold applied plastic and heated-in-place thermoplastic should be used for permanent applications. Thickness is very important when placing paint. Paint should be a minimum of
15 to 18 mils thick wet per application for long term markings. Inspection of paint application is critical. Wet thickness gauges are available from the
Materials and Tests Chemical Lab.
Final wearing surfaces need two applications of
15 to 18 mils wet thickness of paint. A good rule of thumb is
16 gallons of paint per mile for a
4” solid line. The second application is needed to compensate for paint that is absorbed into the pavement during the
first application.
When applying paint for temporary traffic patterns, the line shall be full width and meet the reflectivity requirements in
Article 1205-8 of the Standard Specifications. If the traffic will be left in a pattern for longer than
six months, apply a
second application of paint equal to the
first. Repeat this procedure every
six months. Each layer of paint shall meet the retro-reflectivity requirements of the Standard Specifications.
Within the 30 days of installation, markings should meet the minimum retroreflective values shown in Table 1205-6.
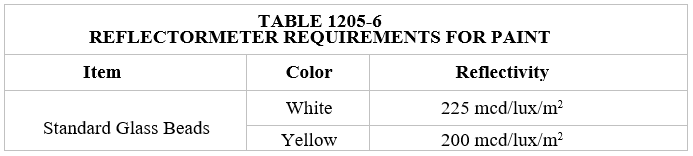
For existing and intermediate pavement markings, retro-reflectivity and the amount of material on the surface are the criteria for maintenance of pavement markings. If the retro-reflectivity readings are below
100 mcd/lux/m2 or there is less than
75%+/- of the pavement marking left on the pavement in any one given area, the pavement needs to be remarked. The Contractor should be compensated for remarking the existing or intermediate pavement markings for maintenance reasons. As a general rule, temporary paint should last
6 to 9 months if placed according to Specifications. If you are not sure if marking
requires maintenance, contact the Division Traffic Engineer, Area Traffic Engineer, and/or the
Signing and Delineation Unit.
There are times when projects will extend into the winter season and the pavement marking contractor will not have an opportunity to place final markings. Winterize the project by placing an application of marking (typically paint) to last the entire winter season or until the final markings are installed and payment should be made to the contractor. However, no payment will be made to the contractor on resurfacing projects where paving is completed more than
30 days prior to the written notification by the Engineer that winterization is required.
ADDITIONAL RESOURCES